The Rise of 3D Printing and Additive Manufacturing
In the fast-paced world of electronics manufacturing, time is of the essence. The ability to develop prototypes quickly and make iterative design changes can be the difference between success and falling behind the competition. Contract manufacturers play a crucial role in this process, and by incorporating 3D printing and additive manufacturing technologies, they can offer significant advantages to their clients.
3D printing and additive manufacturing have come a long way since their inception. Initially used for rapid prototyping, these technologies have evolved to become integral to various industries, including electronics manufacturing. The adoption of 3D printing and additive manufacturing in contract manufacturing is driven by their ability to deliver flexibility, speed, and cost-efficiency.
Advantages of 3D Printing in Contract Manufacturing
1. Rapid Prototyping:
- One of the most significant advantages of 3D printing is its ability to facilitate rapid prototyping. With traditional manufacturing methods, creating prototypes could take weeks or even months. In contrast, 3D printing allows manufacturers to produce prototypes in a matter of days or even hours.
- This speed dramatically accelerates the design phase, enabling engineers to test concepts and make adjustments swiftly. It’s a game-changer for companies aiming to bring products to market quickly.
2. Cost-Efficiency:
- Traditional manufacturing often requires expensive molds or tooling to create prototypes. 3D printing eliminates the need for these costly upfront investments.
- Manufacturers can save not only on tooling but also on material waste. Traditional methods often produce significant material waste, while 3D printing is additive, using only the necessary material.
3. Complex Geometries:
- Many electronics components and devices feature intricate and complex designs that are challenging to manufacture using traditional methods. 3D printing excels in producing such complex geometries.
- Whether it’s a custom-designed casing for a handheld device or a complex bracket for electronic components, 3D printing can handle the job with precision.
Additive Manufacturing for Iterative Design
1. Iterative Design Process:
- Iterative design is a crucial approach to refining products before final production. It involves making incremental changes and improvements to a design based on testing and feedback.
- With 3D printing, manufacturers can easily implement these changes. They can print revised prototypes quickly and affordably, allowing for multiple iterations in a short period.
2. Quick Revisions:
- In electronics manufacturing, design revisions are common, especially during the prototyping phase. 3D printing streamlines this process, as changes can be made digitally and applied immediately to the 3D printer.
- This flexibility ensures that design flaws are caught and corrected early, reducing costly errors later in production.
Practical Applications
Real-world examples illustrate the power of 3D printing and additive manufacturing in contract manufacturing. Companies that embrace these technologies can deliver prototypes and refined designs faster than ever before. This speed-to-market advantage can be a game-changer in industries where innovation is paramount.
One case study involves a contract manufacturer tasked with producing a custom-designed, compact electronic device. Traditional manufacturing methods struggled to create the intricate internal components required for the device’s functionality. By incorporating 3D printing, the manufacturer not only achieved the desired level of complexity but also reduced the time from concept to prototype by 75%.
Challenges and Considerations
While 3D printing and additive manufacturing offer numerous benefits, they are not without challenges. Material limitations, post-processing requirements, and quality control are important factors to consider. Manufacturers need to select the right materials for the job, develop effective post-processing techniques, and implement stringent quality control measures.
Conclusion
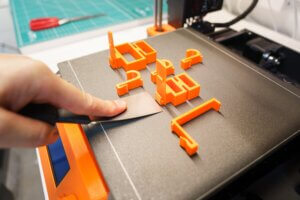
Incorporating 3D printing and additive manufacturing into contract manufacturing processes is a game-changing strategy. It offers rapid prototyping, cost-efficiency, the ability to handle complex geometries, and supports iterative design. By embracing these technologies, contract manufacturers can help their clients stay ahead of the competition in the ever-evolving world of electronics manufacturing. Time is money, and with 3D printing, both can be saved while delivering high-quality results.
As the electronics industry continues to evolve, staying at the forefront of technology is essential. Contract manufacturers that leverage 3D printing and additive manufacturing are poised to lead the way in innovation, speed, and efficiency.