In an era defined by rapid technological evolution, virtual factories and digital twins are emerging as game-changing innovations for the manufacturing industry. By creating digital replicas of physical systems and processes, these technologies offer unprecedented opportunities to optimize operations, enhance quality, and drive strategic business value. For companies looking to stay competitive in an increasingly complex market, the integration of virtual factories and digital twins isn’t just an advantage—it’s becoming a necessity.
This article explores how these cutting-edge tools are transforming manufacturing workflows, improving quality control, and delivering substantial business benefits. From predictive maintenance to sustainability initiatives, we’ll dive deep into the multifaceted advantages and discuss how businesses can harness this technology to secure long-term success.
What Are Virtual Factories and Digital Twins?
At their core, virtual factories and digital twins leverage advanced digital technologies to bridge the physical and virtual worlds. A virtual factory is a comprehensive digital simulation of a manufacturing environment, allowing businesses to analyze, monitor, and optimize their operations in a virtual setting. Digital twins, on the other hand, are real-time digital counterparts of physical machines, processes, or entire systems, reflecting their current state and behavior.
These tools rely heavily on data integration, drawing from IoT sensors, machine learning algorithms, and cloud computing platforms to create accurate, actionable models. The result is a dynamic representation of physical assets and systems that can evolve with real-world changes, enabling smarter decision-making and proactive management.
Virtual factories and digital twins are not limited to manufacturing; their applications extend into logistics, energy, healthcare, and beyond. However, their impact is most profound in industrial settings, where efficiency, precision, and adaptability are critical.
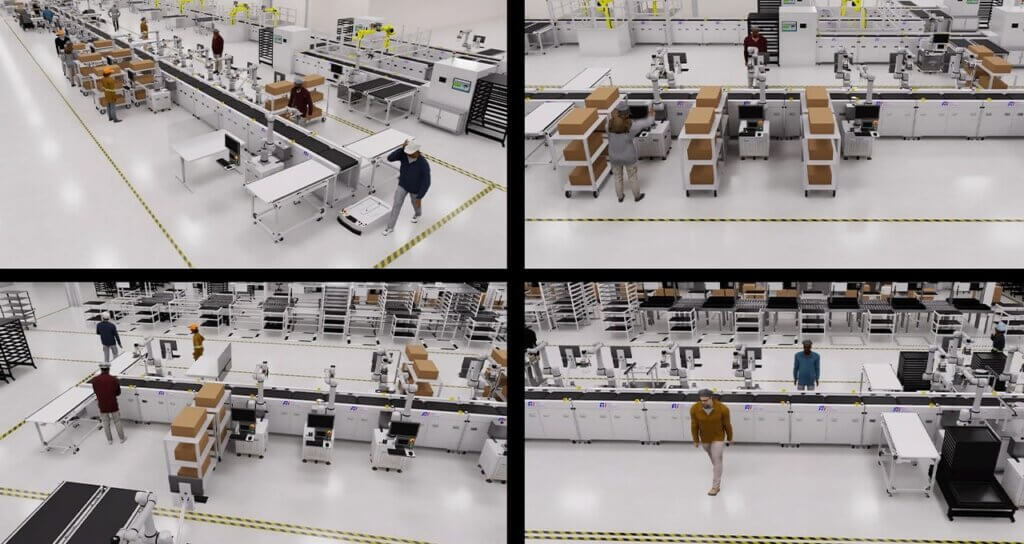
Enhancing Manufacturing Processes
One of the most significant advantages of virtual factories and digital twins lies in their ability to optimize manufacturing processes. By simulating entire production lines, businesses can identify inefficiencies, test new workflows, and predict the outcomes of various scenarios—all without disrupting real-world operations.
Predictive maintenance is a standout use case. Digital twins enable manufacturers to monitor equipment health in real-time, predicting when components will fail and scheduling maintenance before issues arise. This reduces unplanned downtime, extends machinery lifespan, and minimizes maintenance costs.
Moreover, these technologies drive process optimization. For instance, a virtual factory can simulate changes to production schedules, resource allocation, or machine settings to determine the most efficient approach. This level of foresight leads to cost savings, faster production cycles, and reduced waste, making operations more sustainable and cost-effective.
Improving Quality Control
Quality control is another area where virtual factories and digital twins deliver exceptional value. Traditional methods of identifying defects or inconsistencies often rely on reactive processes, detecting issues after they have already occurred. Digital twins, however, provide a proactive alternative by simulating and analyzing products and processes in real-time.
By leveraging advanced analytics, businesses can predict potential defects before they manifest, enabling adjustments during production rather than after the fact. For example, a digital twin of a car assembly line might identify subtle variations in welding precision that could compromise structural integrity, allowing operators to correct the issue immediately.
Additionally, virtual environments support rigorous product design and testing. Engineers can test prototypes under various conditions in a simulated environment, ensuring the final product meets all specifications and quality standards. This reduces the cost and time associated with physical prototyping while enhancing overall product reliability.
The Strategic Business Value
Beyond their technical applications, virtual factories and digital twins offer transformative benefits from a broader business perspective. These technologies empower organizations to become more agile, innovative, and customer-centric, helping them thrive in competitive markets.
1. Cost-Efficiency and ROI:
While implementing these technologies requires an initial investment, the long-term savings often outweigh the upfront costs. Reduced downtime, optimized processes, and higher-quality outputs translate to significant financial gains.
2. Sustainability and Compliance:
Sustainability is a growing priority for businesses worldwide. Virtual factories allow companies to test eco-friendly practices, such as reducing energy consumption or minimizing material waste, without disrupting operations. Digital twins also support regulatory compliance by providing detailed insights into emissions, energy usage, and other environmental metrics.
3. Future-Proofing Operations:
The pace of technological change means businesses must adapt quickly to stay relevant. Virtual factories and digital twins offer the flexibility to test new strategies, adopt emerging technologies, and respond to market disruptions with confidence.
4. Improved Decision-Making:
With access to real-time data and predictive analytics, decision-makers can make informed choices faster. Whether it’s adjusting production schedules, allocating resources, or launching new products, these technologies provide the insights needed to act decisively and strategically.
Challenges and Considerations
Despite their immense potential, adopting virtual factories and digital twins comes with challenges. The initial implementation can be complex, requiring significant investment in technology, training, and infrastructure. Additionally, ensuring seamless integration with existing systems and workflows is critical to realizing their full potential.
However, these challenges are surmountable with a phased approach. Businesses can start small, implementing digital twins for specific machines or processes, and gradually scale up as they gain expertise and confidence. Partnering with experienced technology providers and investing in employee training can further ease the transition.
Conclusion
The rise of virtual factories and digital twins marks a pivotal moment for the manufacturing industry and beyond. By combining cutting-edge technology with practical applications, these tools unlock new levels of efficiency, precision, and innovation. Businesses that embrace them stand to gain a significant competitive edge, not just in manufacturing but across their entire operations.
As the global economy grows more complex, the ability to simulate, predict, and optimize becomes increasingly valuable. Virtual factories and digital twins are not just tools of the future—they are indispensable assets for today’s forward-thinking businesses.